Environment
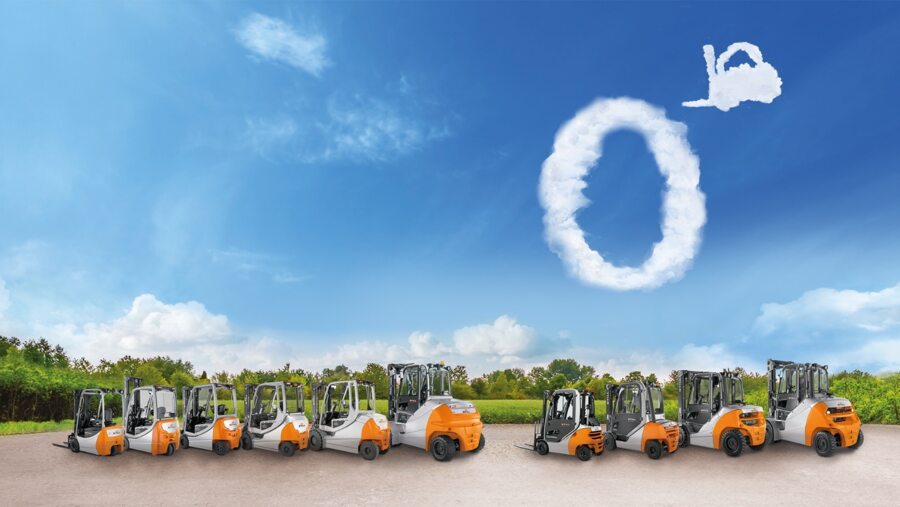
Certified Environmental Management System
Protecting the environment is an important priority for STILL. The company is committed to minimizing the environmental impact of its operations through its HSE management system. Making responsible use of resources and continuously reducing damage to the environment at the local level are a top focus in particular. Its indicator-based approach to environmental management focuses on the areas of energy and greenhouse gas emissions, as well as water and waste.
Under the company’s integrated management policy—which covers sustainability, quality, health and safety in the workplace, the environment, and energy—all managers are required wherever possible to: introduce environmentally-friendly and energy-efficient processes and production procedures; reduce waste; use natural resources such as water, land, and raw materials sparingly and responsibly; avoid and reduce contamination of the air, waterways, and soil; and make active efforts to cut greenhouse gas emissions.
All STILL sites have committed to uphold KION’s Group-wide HSE standard and are also developing specific strategies in line with local requirements. To support these efforts, a designated HSE officer has been appointed for each national subsidiary.
A key sustainability target set out in KION’s corporate strategy is to achieve ISO 14001 (environmental management) certification for all sites by 2024. All production locations and almost all sales organizations are currently certified in line with the latest environmental standards (ISO 14001, ISO 50001, and/or DIN EN 16247). Regular audits provide transparency around the actions taken and lay the groundwork for continually improving sustainability efforts. All relevant energy and environmental management data is also recorded as part of the established HSE management system, thereby supporting effective sustainability management across STILL.
2023 | 2022 | 2021 |
---|---|---|
91% | 89% | 87% |
Energy Management
STILL has set itself the target of increasing energy efficiency and reducing energy consumption per truck. To this end, the company is focusing on renewables and electric vehicles, as well options to optimize the lighting technology in use across its sites. Work has already begun to switch the company’s lighting systems over LED technology and install motion sensors at workstations.
In addition, STILL has completely revamped the energy systems at its administrative building in Hamburg and taken advantage of the increased efficiency of the city’s district heating network to significantly improve its energy footprint and cut its greenhouse gas emissions. Staff are also reminded to use energy responsibly and reduce their energy consumption as part of their mandatory HSE training each year.
Shorter transport distances are also helping to reduce the company’s energy consumption. For instance, customers in the Czech Republic, Slovakia, Hungary, Poland, and Austria are now supplied directly from the warehouse at the new regional service center in Brno in the Czech Republic. The new center has enabled STILL to optimize its transport routes and delivery times and, in doing so, has brought the company closer to its customers as well as further reducing its response times and increasing the availability of its products.
Efforts aimed at conserving energy and using it efficiently go back a long way at STILL. The Hamburg production site obtained its certification according to ISO 50001 (energy management) back in 2013. All of STILL’s energy-intensive production locations are now certified as well and undergo regular audits as part of the current certification cycle.
2023 | 2022 | 2021 | |
---|---|---|---|
Total energy consumption, direct and indirect | 704,729 | 689,477 | 718,734 |
Direct energy consumption | 475,264 | 462,337 | 479,806 |
Diesel (non-renewable) | 258,501 | 248,606 | 243,013 |
Petrol (non-renewable) | 14,289 | 5,463 | 7,300 |
Heating oil (non-renewable) | 13,892 | 14,768 | 15,649 |
Coke (non-renewable) | 74,874 | 72,439 | 93,485 |
Natural gas (non-renewable) | 111,714 | 114,881 | 118,154 |
LPG (non-renewable) | 709 | 963 | 888 |
Biodiesel | 0 | 0 | 827 |
Self-generated solar power (renewable) | 1,285 | 1,297 | 489 |
Indirect energy consumption | 229,465 | 227,140 | 238,928 |
Electricity—externally sourced | 164,955 | 160,316 | 171,312 |
Heating—externally sourced | 64,509 | 66,824 | 67,616 |
Water
STILL ensures that all machinery in use at its premises meets the criteria set out in the German ordinance on industrial health and safety (BetrSichV) and the ordinance on installations for handling water-polluting substances (AwSV). It also carries out regular inspections and monitoring of this machinery.
The company’s plants around the world have measures in place to reduce water consumption, such as water-saving units in sanitary facilities and instructions that company vehicles only be washed when strictly necessary. In addition, the powder-coating system used in STILL’s plants is a state-of-the-art model that generates less wastewater. Automated processes and technologies help to reduce environmental pollution by recirculating and reprocessing the water for pretreatment.
STILL’s operations have very little impact on water quality, to the extent that—other than the use of oil water separators—the wastewater needs no additional treatment prior to disposal. Nonetheless, STILL commissions external analyses at some of its location in order to monitor its wastewater.
The key performance indicators for water withdrawal and wastewater are shown in the table.
2023 | 2022 | 2021 | |
---|---|---|---|
Total water volume | 121,130 | 117,979 | 110,876 |
Groundwater | 450 | 917 | 1,110 |
Municipal water supply | 120,679 | 117,053 | 109,754 |
Other sources | 1 | 9 | 13 |
Climate Protection
As part of international efforts to limit global warning and address the many challenges associated with climate change, STILL and its partners must also take proactive and forward-thinking action to protect the world’s climate. The company works closely with its customers, suppliers, and business partners in many different areas—including energy consumption, efficient use of resources, mitigation of greenhouse gas emissions, and adaptation initiatives—to ensure that it is making a difference within its own operations and beyond.
The KION Group’s climate and energy management policy is based on the Paris Agreement adopted at the United Nations Climate Change Conference in 2015. The Group has committed to achieving the science-based target of reducing its energy-related greenhouse gas emissions (Scopes 1, 2, and 3) by 30% by 2027 in comparison to 2017 levels. A major project to overhaul the existing climate strategy was therefore carried out in 2021.
A key interim outcome from this project is a new set of strategic targets that are fully aligned with the current criteria defined by the Science Based Targets initiative (SBTi). In addition to expanding the scope of the Group’s climate targets to include additional Scope 3 emissions, the Group has also adopted the SBTi’s Corporate Net-Zero Standard as the basis for its target-setting, in order to limit global warming to 1.5 °C above pre-industrial levels in line with the Paris Agreement.
Under the new targets, the KION Group plans to significantly cut greenhouse gas emissions across its value chain by 2030 (near-term) and continue on the path to achieving net zero by 2050 at the latest (long-term, Scopes 1, 2, and 3). Its strategy includes carbon dioxide (CO2)—the biggest contributor—as well as other greenhouse gases such as methane, nitrous oxide, hydrofluorocarbons, sulfur hexafluoride, and nitrogen trifluoride, wherever applicable and viable. The new targets also bring the Group in line with new regulations such as the European Green Deal and the EU Taxonomy.
To facilitate the effective and efficient management of its greenhouse gas emissions and energy usage, the Group has introduced a comprehensive climate management system which covers both its own operations and other parts of its wider value chain—from production to the use phase and even re-use at the end of the current product life span. Data on greenhouse gas emissions is collected and presented within the system in accordance with the internationally recognized Greenhouse Gas Protocol.
With respect to Scopes 1 and 2, the KION Group is working to further reduce emissions as well as energy consumption within its own operations by improving processes and using energy-efficient technologies. Ongoing measures initiated through the local energy or environmental management systems link into central initiatives. These include:
- Switching to energy-efficient motors
- Using waste heat in production
- Optimizing heating systems and building infrastructure
- Using LED technology
- Optimizing transport in sales and service
These measures are combined with centralized initiatives, such as efforts to convert the company’s own vehicle fleet to low-carbon drive technologies, source more energy from renewables, and explore additional self-generation options for renewable energy.
Efforts to reduce Scope 3 emissions are based on the categories identified as part of a materiality analysis. By far the biggest of these categories—and therefore the priority for action—are the emissions generated by the company’s products during the use phase. In addition to improving the product design, the company also educates customers about sustainability factors to consider when choosing a solution, ways they can use their products more energy-efficiently, and their options for using them in combination with renewables. The second biggest category—and another key focus alongside Scope 1 and 2 emissions—are emissions from purchased goods and services; that is, emissions associated with suppliers and materials. To enable it to address its top Scope 3 emissions categories, the KION Group is gradually introducing findings from life cycle analyses; data on materials, suppliers, and customers; and engagement initiatives involving partners in the value chain (for more information, see KION Sustainability Report 2023).
2023 | 2022 | 2021 | |
---|---|---|---|
Scope 1, market based | 34,357,546 | 33,470,453 | 35,098,796 |
Scope 2, market based | 3,940,772 | 3,822,547 | 4,067,903 |
Scope 3.31, location based | 10,405,374 | 10,037,979 | 10,332,681 |
Total emissions | 48,703,692 | 47,330,979 | 49,499,380 |
[1] Indirect (upstream) fuel and energy-based greenhouse gas emissions
Measures to Cut CO2 Emissions
Modernization work at the Hamburg plant in 2023 saw the replacement of two CO2 laser cutting machines with fiber laser systems that are significantly more eco-friendly and efficient. This project has reduced power consumption at the plant by approximately 156,000 kWh, while also saving 67 t of CO2 due to the fact that the laser in the new systems is no longer gas generated.
In addition to reducing its own greenhouse emissions, STILL also supports selected climate protection projects in order to offset its emissions through climate protection certificates (or carbon credits). One supported project generates renewable energy from sawdust—a waste product from the production of raw material for the paper industry. The sawdust is used as biomass for generating steam, which in turn serves as an energy source for the production of more raw material. This regenerative system therefore enables fossil energy sources to be replaced as a heat source. The biomass project is one of the only climate protection projects in Europe to have been awarded Swiss Climate’s “Gold Standard” and enabled 26,475 tons of CO2 to be offset in Switzerland in 2022.
Another offsetting project supported by STILL is “PLANT-MY-TREE.” One of the areas to be regenerated as part of this project is a reforestation area in Hohenaspe, near Itzehoe in northern Germany, where the first of 1,000 trees was planted in 2020. This tree and others will continue to grow and absorb harmful emissions for at least 100 years as part of “STILL’s woodland.” Moreover, customers at two of the company’s main branches in Hanover and Bielefeld can get involved. Each time these customers order a new electric forklift truck as a replacement for an internal combustion truck, they receive a personalized tree planting certificate as a token of thanks for their custom. They can then display this certificate at their premises as evidence that they are a company that takes its environmental responsibilities seriously.
All German companies in the Group also offer their employees the opportunity to use a portion of their gross pay to lease a bicycle, which they can then use outside of their commute as well. The bike scheme is a benefit requested by many staff and, at the same time, is an opportunity for STILL to promote sustainable transport more widely.
STILL is also taking action with respect to its fleet of company vehicles. In spring 2022, STILL Switzerland signed up to the DKV Climate Card from the DKV Mobility Group, meaning that more than 90% of the company’s vehicle refueling in Switzerland is now climate neutral. STILL Nordic Markets (Denmark, Sweden, and Norway) also introduced a new regulation in 2022, which stipulates that all company vehicles must be hybrid or electric. The vehicle fleet in Hamburg was converted to vehicles with an electric drive in 2023. Many of the company’s locations are reviewing the potential to convert their fleets as well and rolling out these changes on a successive basis.
Additional Emissions Monitoring
Most of STILL’s premises are located in industrial areas where there are no local residents. Ongoing checks and measurements have confirmed that no external soundproofing is required; however STILL does have internal noise reduction measures in place. Noise levels are assessed across all workplaces and the health and safety and environmental protection department maintains and regularly updates a register of noise measurements taken. Risk analyses are conducted to identify the most effective measures to protect employees against noise-induced hearing loss, including warning signs displayed across all production sites and ear defenders supplied free of charge. Acoustic enclosures are also erected around loud machinery and soundproofing walls installed.
Filter systems are installed at relevant sites to limit the emissions generated by our plants with the aim of protecting the environment as well as our own employees from exposure to hazardous substances. STILL’s iron foundry, Eisengießerei Dinklage GmbH, is an example of a plant that is fitted with highly effective filter systems to reduce the amount of fine dust emitted into the atmosphere to an unavoidable minimum.
2023 | 2022 | 2021 | |
---|---|---|---|
Other significant airborne emissions—total | 1,928,112 | 1,010,299 | 1,015,238 |
Carbon monoxide (airborne emissions, CO) | 1,884,679 | 947,275 | 947,275 |
NOx | 3,678 | 3,765 | 3,765 |
SOx | 5,141 | 18,989 | 18,989 |
Volatile organic compounds (VOC) | 34,220 | 36,226 | 40,978 |
Particulate matter (PM) | 386 | 4,127 | 4,288 |
Other airborne emissions | 8 | 8 | 34 |
Efficient Use of Resources
Under the Group-wide HSE Standard, all local Group companies—including STILL—must have processes in place for recycling and re-using their waste. Refurbishing trucks for re-sale is a positive solution for many reasons, not least the fact that it saves valuable resources and reduces waste. Used trucks are therefore playing an increasingly important role in STILL’s sustainability strategy, since they significantly reduce the company’s CO2 emissions and, in turn, its carbon footprint.
In the 2023 reporting year, STILL put nearly 13,000 used trucks back into circulation. If the trucks are not suitable for re-sale by STILL, another reputable KION Group company—BlackForxx—markets them to third-party dealers worldwide.
STILL also offers its customers the opportunity to rent trucks in order to cover peak production periods, help with events, or replace trucks that are out of service. In fact, many companies are increasingly turning to rental options as a way of using resources more responsibly—modern fleet management without a fleet!
Another important focus for STILL in terms of using resources responsibly is to find ways to replace critical materials and hazardous substances with less critical and hazardous alternatives. This applies to both raw materials and the operating materials used in production that are not part of the end product itself. For instance, in recent years, the hazardous substance methylene chloride, which was typically used for cleaning out paint sprayers, has been replaced with a less hazardous alternative. Likewise, the company’s painting lines are now cleaned down using a less hazardous product.
In addition, STILL Hamburg has two additional projects underway aimed at reducing its consumption of (hazardous) materials. The first project consists of substituting the lead used in the soldering processes for its mechatronics work, while the second involves switching from single-use spray cans to reusable spray cans in its maintenance work.
Waste Disposal
STILL is consistently working to cut its waste volumes, notably by reducing the amount of packaging in use.
In line with the KION HSE Standard, different types of waste are separated into clearly labeled containers that can be easily accessed by large refuse collection vehicles. The waste disposal area is suitably equipped and has warning signs in place to prevent waste from being blown around the site in bad weather and mitigate leaching and contamination of the soil in case of heavy rainfall.
The waste disposal company contracted by STILL in Hamburg provides the following recycling and disposal services in accordance with the German Circular Economy Act (KrWG):
- Recycling and recovery of organic waste
- Reprocessing of sludge and residue from kitchen grease trap
- Recycling and recovery of inorganic waste—i.e. reprocessing of slurry and emulsion from operating processes
- Waste exchange, so that the waste can be processed—for example, conditioned or dried—and inputted into another end recycling or recovery system
All employees are also encouraged to play their part in reducing waste. The company canteen at STILL in Hamburg is participating in the RECUP and REBOWL initiative, Germany’s largest reusable packaging system for take-away food and drink.
2023 | 2022 | 2021 | |
---|---|---|---|
Hazardous waste for disposal | 1,049 | 1,248 | 1,525 |
Incinerated | 52 | 63 | 63 |
Sent to landfill | 639 | 697 | 703 |
Other disposal method | 359 | 487 | 759 |
Non-hazardous waste for disposal | 4,926 | 6,896 | 8,838 |
Incinerated | 217 | 179 | 268 |
Sent to landfill | 3,734 | 6,129 | 57 |
Other disposal method | 975 | 589 | 8,513 |
2023 | 2022 | 2021 | |
---|---|---|---|
Hazardous waste for recycling/re-use | 3,542 | 3,378 | 3,057 |
Recycled | 2,762 | 2,640 | 2,608 |
Processed ready for re-use | 66 | 19 | 206 |
Other method | 714 | 718 | 243 |
Non-hazardous waste for recycling/ re-use |
16,558 | 13,723 | 15,267 |
Recycled | 14,989 | 12,624 | 13,838 |
Processed ready for re-use | 655 | 659 | 347 |
Other method | 914 | 440 | 1,082 |
Further initiatives
The mandatory HSE training completed by staff each year covers a range of environmental, climate, and energy management topics that are relevant for the business, including energy consumption, water usage, waste separation, and the risks posed by climate change.
2023 | 2022 | 2021 |
---|---|---|
90% | 84% | 79% |
The increased awareness of environmental issues among staff can be seen in the large numbers of environmental initiatives organized across the business:
- Nearly all units of the business are now working within the framework of the ISO 14001 certification, with the final entities set to following in 2024.
- Every year at Easter, the “Recycling Bunny” visits employees in Switzerland with ideas, tips, and suggestions relating to sustainability and health. The more that is recycled, the less that needs to be produced, and that reduces emissions and saves lots of valuable natural resources.
- In March 2023, STILL employees were asked to donate their old cellphones, tablets, and accessories as part of World Recycling Day. Around 80% of the components in a cellphone can now be recycled and used to replace material that would otherwise have to be sourced from nature. The donated devices were used to support the “Handys für Hummel, Biene & Co” (Cell Phones for Busy Bees and Friends) initiative run by the German Nature And Biodiversity Conservation Union (NABU), which has been working since 2006 to promote professional cellphone recycling and ensure that the materials from electronic devices are fed back into the material cycle. A total of more than 500 devices, including cellphones, tablets, headphones, and power adapters, were collected in the NABU boxes at the German sites of KION Group AG. Nearly 200 of these cellphones and accessories came from the boxes at STILL. While this campaign specifically focused on personal devices, STILL is also working to ensure devices for work purposes can be reused or used for longer. For example, outdated or faulty company cellphones have been collected at German sites for several years now and are sent to a service provider that recycles the devices or refurbishes them before putting them back into circulation.
- STILL Poland continued its “A tree for a forklift” campaign in 2023 for all of the self-propelled trucks sold during the calendar year. In line with the campaign’s premise, STILL Poland committed to planting one tree for every truck sold during the calendar year. Since planting is only possible during spring and fall, the environmental stats for the scheme are based on the total number of trees pledged, rather than the number actually planted to date. The campaign has pledged to plant 4,829 m2 of woodland in all, as well as absorbing 26,106 kg CO2 and offsetting 252,358 kg of paper consumption.
Idea Management
Idea management—i.e. the process of collecting suggestions from all staff in order to continually improve the business—has been a central fixture in STILL’s company culture for many years. Quality standards, productivity, and employee satisfaction are thus improved across the company based on the insights and experiences of the whole staffing body. The aim is to leverage untapped potential for improvement and incorporate these areas into the ongoing improvement process for the entire product and service portfolio, which comprises both production and work processes as well as working conditions, including health and safety and environmental protection. Ideas for improvement are assessed by an expert in the relevant field against a defined set of criteria and given a score, with prizes awarded for the best-scoring ideas.
In 2022, STILL ran its first idea management initiative with a focus on environmental sustainability. Over a period of three weeks, employees submitted their suggestions on how to make KION more sustainable. The questions posed included: How can we reduce our energy consumption? How can we save on raw materials and components, or better re-use them as part of a closed-loop cycle? How can we optimize our supply chains and transport routes to make them more environmentally friendly? And, how can we reduce waste and improve recycling? A panel then selected the ten best suggestions and awarded prizes to the three ideas with the biggest environmental impact. A total of 354 employees submitted suggestions and in 2022 STILL put three of its staff’s ideas into practice. This included cutting the volume of plastic waste associated with the delivery of cylinders to production sites by working together with the supplier to have the cylinders delivered in bundles, thereby reducing the amount of plastic packaging. The company also implemented another idea from the campaign, which consisted of printing only one delivery note for spare parts rather than two, saving a large amount of paper and toner in the process.
An idea that looks at sustainability from a social perspective was also put into action outside the campaign and involves fruit harvested in the local region. The produce is processed by people who have disabilities or are disadvantaged to make fruit juice, which is then available for purchase in the canteen.