Health and Safety
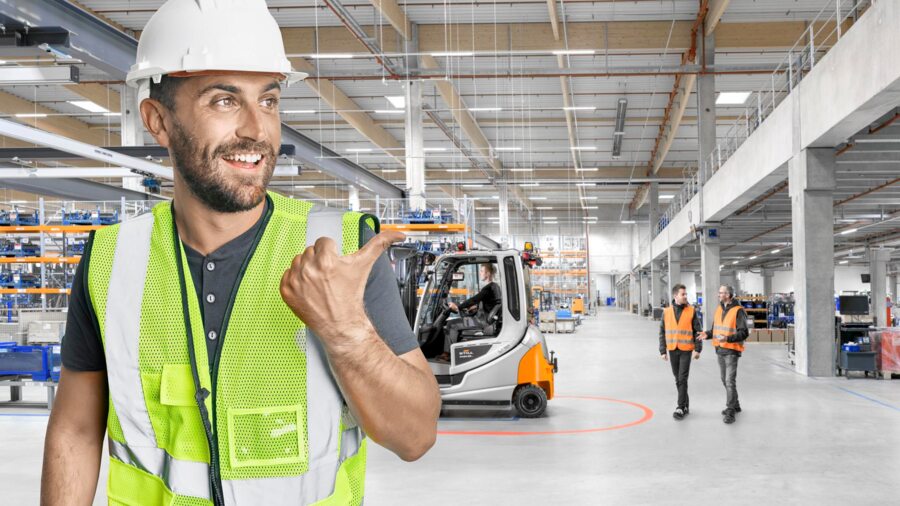
Health and Safety
STILL has set itself some ambitious health and safety targets. One of the key sustainability aims set out in KION’s corporate strategy is to reduce the accident rate in the workplace. As part of these efforts, STILL established an integrated health, safety, and environment management system, which was set up and certified for the first time in 2013. New job roles were also created and skilled experts appointed to respond to increasing requirements and ensure the smooth roll-out of the necessary changes and initiatives.
Introduced in 2019, the Group-wide “golden rules of occupational safety” provide helpful guidance on specific actions that managers and employees can take to reduce the rate of accidents. These rules are communicated to staff across the company and have been instrumental in continually improving workplace safety standards at STILL.
Another Group-wide policy, the KION HSE Standard, was also updated and rolled out in 2022. This standard defines the basic requirements and processes that must be observed across the Group. Its contents reflect the specific requirements of different job roles and regions and are updated to reflect changing business conditions as needed.
These Group-wide standards provide the framework for STILL’s operational HSE activities. The company’s detailed regulations often go beyond the basic health and safety standards required by law, because STILL is committed to creating the safest-possible working environment for its employees, while at the same time minimizing its environmental impact.
Health and safety are integral elements of the corporate strategy, and this also extends to external business partners working at STILL as well as visitors to the company. One of the main focal points is coordinating related efforts in a professional way to provide safe conditions for external and in-house employees as well as visitors, and to ensure that applicable safety regulations are observed.
Health Protection
STILL relies on a series of interconnected measures to protect the health of its staff to the greatest possible extent, increase their health awareness, and reduce days lost due to illness. These include healthy workplaces designed in line with the German Occupational Health and Safety Act (ASiG), well-organized and effective first-aid systems, medical consultations and examinations, preventive healthcare services, and addiction support.
STILL’s system for managing occupational health includes the following:
- EAP, a service providing anonymous advice and assistance to employees in any life circumstances
- Training for managers on healthy leadership
- A healthy menu in the company canteen and initiatives promoting a healthy diet
- A highly effective system for integrating new employees into the company
- Sports activities
- Health days and presentations
- Support in attaining a stronger mental balance
- Option to see a physiotherapist on-site at the plant
Medical care at STILL is provided by the company doctor and a team of medical assistants. First aiders, paramedics, and an in-house medical unit work as a team to ensure first aid can be provided in all instances. Together with a team of safety specialists, these staff members ensure that STILL has expertise in place to effectively meet the occupational health and safety requirements set out in law.
At the end of August 2022, a pilot project was launched in partnership with a rehabilitation provider to deliver basic workplace physiotherapy services. These activities had an extremely positive impact for both the workplace and staff and were made a regular fixture of the business health management system in January 2023.
Safety: Prevention Rather Than Response
The HSE management system covers all relevant workplace safety issues and ensures that staff have a clear understanding of the most important safety processes. This helps increase awareness and lays the foundation for safety-conscious behavior in the workplace on the part of all staff and managers. The HSE management system is underpinned by a series of interconnected policies, including STILL’s policy for handling hazardous substances and agents, emergency procedures, and a process for analyzing accidents and near-misses.
Regular and detailed risk analyses are conducted for all STILL activities and workplaces, including both internal production and office facilities and the external working environments encountered by service technicians on-site at customer premises. The aim of these analyses is to ensure that employees come to work healthy and return home healthy—without suffering any preventable damage to their health either during or after the end their careers. In addition to hazards relating to physical, chemical, or ergonomic aspects, the risk assessment includes an analysis of psychological stressors in the workplace. The risks posed to employees’ mental health by stress, mental fatigue, monotony, mental saturation, and emotional exhaustion, as well as the concrete actions needed to improve the situation are identified in the course of a systematic analysis.
2023 | 2022 | 2021 |
---|---|---|
89% | 89% | 93% |
Handling Hazardous Substances and Agents
Hazardous substances and agents must be handled with care at all times. For this reason, the company takes care to ensure that hazardous substances are reduced to a minimum and less hazardous alternatives are always selected before a substance is used. An interdisciplinary hazardous substances committee confers on the introduction of new substances, taking into account the safety data sheets, legal aspects, and usage instructions, as well as the respective conditions on site. Approved hazardous substances and agents are listed and monitored in a database.
All employees that work with hazardous substances and all individuals that could come into contact with these substances are given verbal instruction in how to use the substance safely, both before they use it for the first time and at least once per year after that. This training covers the potential risks, safety precautions, and rules during use as well as actions to be taken in case of an emergency. Where appropriate, practical exercises also form part of the training. If a health and safety risk cannot be eliminated by applying technical or organizational measures, personal protective equipment (PPE) must be used.
Relevant production processes are analyzed by taking regular measurements to monitor exposure to hazardous substances or working conditions, such as fumes, noise, or chemicals. STILL is gradually replacing its manual welding stations with robotic welding systems, as well as installing ventilation systems at steel construction sites and improving the soldering processes for its mechatronics work, in order to continually improve the standard of protection against exposure to hazardous substances for its employees. The potential for exposure to emissions or operating and auxiliary materials is also a key factor in the planning and procurement of new machinery and plants.
Emergency Procedures
How employees respond to an emergency situation (such as an accident, fire, or other unforeseen event) has a significant bearing on the incident outcome. STILL has therefore devised an emergency procedure to ensure these situations are handled quickly, appropriately, and in a well-organized manner.
Up-to-date emergency plans—with a bulleted list of the key action points—are therefore available at all STILL sites and are displayed in a clearly visible location, such as close to the entrances or alongside fire extinguishers. Responsibility for creating these emergency plans lies with the site management, and they are supported in this task by their team of safety specialists and, where available, their fire officers.
Change Management
Change management is a proven process for monitoring HSE risks and dangers resulting from changes to facilities, operational procedures, or staffing within an organization. Right from the initial planning phase, STILL is committed to assessing and minimizing any potential risks in terms of health and safety, quality standards, energy procurement, and environmental protection.
To this end, the company has an established process in place for workplace approvals, which governs the procedure for approving new workplaces, machinery, and plants as well as equipment and materials. This process is designed to support managers in deciding whether a new workstation, machinery, plant, or operating material can be commissioned without compromising the health and safety of employees.
Process for Analyzing Accidents and Near-Misses
Accidents and near-misses are recorded and carefully analyzed across all sites using a variety of different tools. All the parties affected—persons involved in the accident, their line manager, the HSE department, and site management—are questioned in detail about what happened and the surrounding circumstances, and the cause of the accident is identified based on this information. A cause-and-effect (Ishikawa) diagram is also created, and appropriate action is defined.
In Switzerland, for example, a specialist reporting app has been introduced to help staff learn lessons from unsafe and dangerous situations. Employees are encouraged to report risky or dangerous situations (where an accident was narrowly avoided) using the online app, so that action can be taken to prevent similar situations in future. Details of the situations reported and actions taken are available for all employees to view on the intranet.
Training
All STILL employees receive regular health and safety training. Before starting work, new employees must complete mandatory training in the specific risks associated with their workplace/role. Employees who miss the training must be briefed immediately on returning to work. Information on the hazards relating to the respective role, corresponding protective measures, as well as actions to take in hazardous situations are identified in the course of a discussion between the line manager and employee, and behavior that is conducive to health and safety is encouraged.
The respective manager is responsible for carrying out the training. Safety training is tailored to the respective workplace and covers the specific risks encountered there as identified in the risk assessment, as well as any operational lessons learned. The training may include the following topics:
- Company HSE policy
- Employee and manager responsibilities with respect to safety
- Emergency protocols (raising the alarm, escape routes, assembly point, etc.)
- Procedure for reporting accidents within the company
- Contact information in case of emergencies
- First aid and emergency equipment
- Fire procedure and firefighting equipment
- General company safety precautions
- Alcohol and smoking policies
- Availability and use of personal protective equipment (PPE)
- Safe handling of hazardous substances
- Safe use of machinery, cranes, and forklift trucks
- Company’s environmental obligations
- Potentially explosive areas
- Performance of manual tasks
- Wellbeing and hygiene
- Safe use of hand-held tools and portable electrical devices
- Safety awareness, incentives, and training to address specific areas of conduct
Training is also provided as required in response to specific events, for example, following accidents or near-misses.
2023 | 2022 | 2021 |
---|---|---|
100% | 99% | 100% |
Management of External Contractors
The system for managing external contractors is designed to minimize risks that could arise due to work performed by external contractors, thereby furthering efforts to continually improve health and safety and environmental protection. Trained contractor coordinators work together with the contractor to ensure the required work is performed in line with STILL’s safety strategy and to check that the agreed working conditions are maintained while the work is carried out. External contractors must use STILL’s HSE information sheet as the basis for providing their employees and any subcontractors with training on safe working practices at STILL and the specific conditions at the work or construction site prior to commencing work. This training must also be provided each time there is a change in personnel. Staff who are employed on a continual or recurring basis are to receive refresher training every year.
Additional Measures
STILL has also introduced the following measures and initiatives to improve workplace safety standards at its sites:
- An HSE monitor was introduced in the German service organization so each manager can record their technicians’ safety performance in real time and evaluate the near-misses they report, for example.
- Quentic, an HSE software solution used to record all data of relevance to occupational safety, is also being rolled out at a growing number of sites outside Germany. Automated interfaces and a streamlined login process ensure data is up to date while providing for a convenient user experience.
- In June 2023, STILL Hamburg invited all employees to take part in a safety action day on the theme “Profis arbeiten immer sicher” (Professionals always put safety first). Employees had the chance to refresh their skills around safety at work, at home, and in their free time by visiting the event’s six different stations, which featured exhibits demonstrating the importance of being alert and cautious when using heavy equipment, sharp objects, or hazardous substances.
- On June 27, 2023, STILL launched SAFETY STARTS WITH YOU, a training program aimed at STILL’s service technicians around the world. Four short video clips show two employees encountering typical unsafe situations in the service setting, which they have to identify and deal with promptly. The videos are available in the respective local languages and are assigned to employees as mandatory e-learning.
- Since 2015, STILL has been using a psychological approach that centers on discussions and meaningful communication and is designed to change attitudes and behaviors. This approach aims to help everyone involved avoid workplace accidents wherever possible and create a sense of shared responsibility for safety.
- An increasing number of employees who have received HSE training are being recruited in smaller units as well, even if this area only represents part of their work.
Safety officers meet regularly with management staff, the HSE department, and the works council to share information about the latest health and safety developments and discuss various topics relevant to the company’s business operations.
2023 | 2022 | 2021 |
---|---|---|
87% | 87% | 80% |
Workplace Safety Key Performance Indicators
The lost time injury frequency rate is the key performance indicator (KPI) used to measure progress towards the sustainability target of reducing workplace accidents and days lost due to illness (LTIFR1). The LTIFR represents the number of workplace accidents recorded, per one million hours worked during the reporting period, that resulted in an employee being off work for at least one day. The target is to reduce this KPI—and consequently the accident frequency rate—by at least five percent per year.
2023 | 2022 | 2021 |
---|---|---|
9.6 | 12.3 | 15.6 |
[1] Number of accidents per one million hours worked that resulted in an employee being off work for at least one day.
2023 | 2022 | 2021 | |
---|---|---|---|
Employees including apprentices | 141 | 168 | 203 |
Employees with fixed-term contracts | 8 | 13 | 8 |
Contractors, guests, other | 0 | 0 | 1 |
[2] Number of workplace accidents that resulted in an employee being off work for at least one day.
Audits and Certifications
The purpose of HSE certifications and regular audits is to ensure that all internal and external HSE requirements are being met and that rapid action is taken as necessary to address cases of non-compliance. To this end, all production locations and almost all sales organizations are certified in line with current labor and environmental standards (ISO 14001, ISO 4500, and ISO 50001). Feedback from the certification and audit process also provides valuable strategic insights that help inform future actions and initiatives.
2023 | 2022 | 2021 |
---|---|---|
91% | 89% | 87% |
A report detailing the activities of the different HSE departments within the KION Group Operating Units is produced each year based on data collected using the software program Cority. Regular reports are also published on progress achieved with respect to labor standards. As well as keeping the management informed about the latest progress, these reports are instrumental in defining targets and shaping future actions.
Internal reporting also provides the basis for the systematic analysis of current health and safety standards and potential areas for improvement. This includes the annual risk assessment based on KION’s HSE standards as well. The results of this risk analysis are used to define actions that local organizations can take to prevent injuries, illness, and damaging impacts on the environment.
In addition, all sites in Germany undergo an external HSE risk analysis every two years to verify that they are compliant with the health and safety standards set out in law.
STILL pursues a focused and coordinated approach to achieving its HSE targets in close consultation with the responsible Group management. This process is supported, in particular, by the audits conducted as part of its HSE management certification and to ensure compliance with the Group’s own HSE standards. In addition, the company conducts its own internal HSE audits across all of its departments each year.
By taking these steps, STILL lays the groundwork for a process of continual improvement, which ultimately fosters a positive HSE culture among all its employees.